Lets talk and learn something from this Lucky/ Unlucky event~
First of all, I am so glad that everyone on that flight made it back alive~
Thanks to them Airbus revised the fuel imbalance and fuel leak procedure~
我又一如以往base on final report講下~
黑字係report~
藍字就係我ge個人想法~
Actually Airbus modified the fuel leak procedures after this incident; so thanks to this, it makes our operation safer.
Pictures credited to the final report
Accident Investigation Final Report
All Engines-out Landing Due to Fuel Exhaustion
Air Transat Airbus A330-243
24 August 2001
Summary:
On August 24, 2001, Air Transat Flight TSC236, an Airbus 330-243 aircraft, was on a scheduled flight from Toronto Lester B Pearson Airport, Ontario (CYYZ), Canada to Lisbon Airport (LPPT), Portugal with 13 crew and 293 passengers on board. At 05:33, the aircraft was at 4244N/2305W when the crew noted a fuel imbalance. At 05:45, the crew initiated a diversion from the flight-planned route for a landing at the Lajes Airport (LPLA), Terceira Island in the Azores. At 05:48, the crew advised Santa Maria Oceanic Control that the flight was diverting due to a fuel shortage. At 06:13, the crew notified air traffic control that the right engine (Rolls-Royce RB211 Trent 772B) had flamed out. At 06:26, when the aircraft was about 65 nautical miles from the Lajes airport and at an altitude of about FL 345, the crew reported that the left engine had also flamed out and that a ditching at sea was possible. Assisted by radar vectors from Lajes air traffic control, the crew carried out an engines-out, visual approach, at night and in good visual weather conditions. The aircraft landed on runway 33 at the Lajes Airport at 06:45. After the aircraft came to a stop, small fires started in the area of the left main-gear wheels, but these fires were immediately extinguished by the crash rescue response vehicles that were in position for the landing. The Captain ordered an emergency evacuation; 16 passengers and 2 cabin-crew members received injuries during the emergency evacuation. The aircraft suffered structural damage to the fuselage and to the main landing gear.
Summary無comment~
1.1.1 History of the Flight On August 24, 2001, Air Transat Flight TSC236, an Airbus 330-243 aircraft, was on a scheduled flight from Toronto Lester B Pearson Airport, Ontario (CYYZ), Canada to Lisbon Airport (LPPT), Portugal with 13 crew and 293 passengers on board. The Captain was carrying out the pilot flying (PF) duties for this flight. TSC236 was planned to depart CYYZ at 00:10 UTC1 , with 47.9 metric tons of fuel , which included a 5.5 tons over and above the fuel required by regulations for the planned flight; the actual take-off time was at 00:52 with a reported 46.9 tons of fuel on board. According to the crew, the flight progressed normally until after crossing 30º West and at 05:03 when they observed unusual engine oil indications on the Number 2 (right) engine (Rolls-Royce RB211 Trent 772B) .
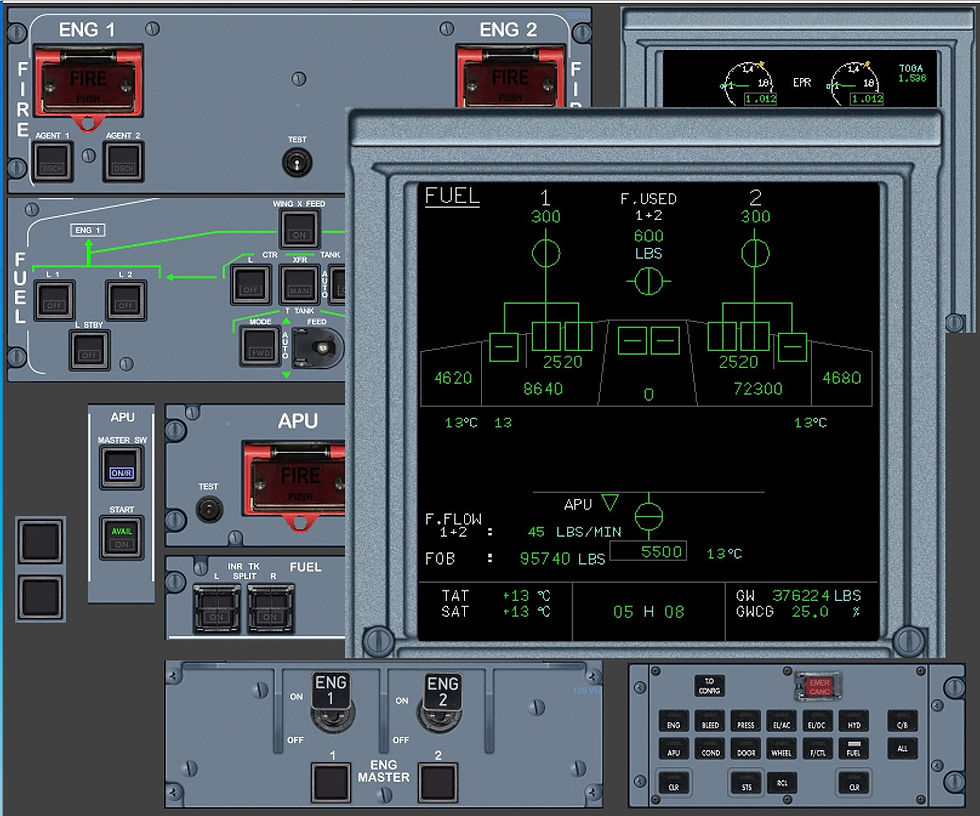
The ENGINE Electronic Centralized Aircraft Monitoring System (ECAM) page was manually selected by the crew, and the oil indications were communicated by high-frequency (HF) radio to the dispatcher at the company’s Maintenance Control Centre (MCC) at Mirabel Quebec, Canada. At approximately 05:33, an advisory ADV message was displayed on the Engine/Warning Display (EW/D). The crew noticed the ADV and deselected the ENGINE ECAM page. This action resulted in the Fuel ECAM page being displayed and the crew becoming aware of a fuel imbalance between the left and right inner-wing tanks. To correct the imbalance, the crew selected the cross feed valve OPEN and the right-wing fuel pumps OFF in order to feed the right engine from the left-wing tanks.
Normally when fuel imbalance occurs, we need to figure out why does it happen, before correcting to imbalance. It is because engines shall consume fuel at similar rate; and imbalance won't just happened.
At 05:45, the fuel on board had reduced to below the minimum required fuel on board to reach Lisbon, and the crew initiated the diversion to Lajes Airport (LPLA) on Terceira Island in the Azores. By 05:48, the crew advised Santa Maria Oceanic air traffic control that the flight was diverting due to a fuel shortage; the fuel on board had reduced to 7.0 tons. In attempts to resolve the sudden and unexplained reduction in the fuel quantity readings, the crew asked the cabin crew to visually check the wings and engines for a possible fuel leak: the visual check did not reveal any evidence of a fuel leak. At 05:54, in reaction to the continued abnormally high rate of reduction in the fuel-on-board quantity reading, the crew selected the right-wing fuel pumps to ON and the left-wing pumps to OFF. These selections established cross feed of the fuel in the right wing tanks to both engines. According to the crew, the cross feed from the right tank was established to use up the fuel from the right wing and to counter the possibility that the fuel loss was the result of a leak in the right wing tanks.
The crew then contacted MCC on HF, advising the dispatcher of the inexplicable low fuel quantity readings. At this time, fuel on board was 4.8 tons, or 12 tons below the planned quantity. The crew reported that they could not determine what the problem was that the fuel indication was continuing to reduce, and that the apparent fuel leak was happening in the right-wing inner tanks. At 05:59, during the dialog with MCC, the crew reported that the fuel quantity had further reduced to 1.0 tons in the right tanks and 3.2 tons in the left tanks. MCC asked whether the fuel loss might be a leak in the left engine. In reaction to this suggestion, the Captain momentarily reselected cross feed from the left tanks. The crew stated that all fuel pumps were selected ON when the fuel remaining was 1.1 tons. At 06:13, when the aircraft was at FL390 and 150 miles from Lajes, the right engine flamed out.
The crew notified Santa Maria control that the engine had flamed out and that the flight was descending. At 06:15, the crew reported to air traffic control that the fuel on board had reduced to 600 kilograms. At 06:23, the First Officer declared a “Mayday” with Santa Maria Oceanic Control, and at 06:26, when the aircraft was 65 nautical miles from the Lajes airport and at an altitude of about FL 345, the left engine flamed out. The ALL ENG FLAME OUT procedure was completed by the crew and an engines-out descent profile was flown towards Lajes. At 06:31, the flight was transferred to Lajes Approach Control. Assisted by radar vectors and flashing of the runway lights, the aircraft arrived about 8 miles off the approach end of runway 33 at approximately 13 000 feet on a track of about 270°. The Captain advised Lajes that he was conducting a left 360-degree turn in order to lose altitude. During the turn, the aircraft was configured with leading-edge slats out and landing gear down for the landing. S-turns were conducted on final to lose additional altitude. At 06:45, the aircraft crossed the threshold of runway 33 at about 200 knots, touched down hard 1 030 feet down the runway, and bounced back into the air. The second touchdown was at 2 800 feet from the approach end of the runway, and maximum braking was applied. The aircraft came to a stop 7 600 feet from the approach end of the 10 000-foot runway. After the aircraft came to a stop, small fires started in the area of the left main-gear wheels, but these fires were immediately extinguished by the crash rescue response vehicles that were in position for the landing. The Captain ordered an emergency evacuation. Fourteen passengers and two cabin-crew members received minor injuries, and two persons received serious injuries during the emergency evacuation. The aircraft suffered structural damage to the fuselage and to the main landing gear.
1.1.2 Summary of Related Engine Maintenance Events
On 15 August 2001, during a routine inspection of the Air Transat Airbus 330-243, Serial Number 271 aircraft, metal chips were found on the master chip detector in the oil system of the right (No #2) engine (Rolls-Royce RB211 Trent 772B, # 41075).

On 17 August 2001 there was a second incidence of metal particles in the oil system, and because the origin of the metal could not be identified, Air Transat decided to replace the engine. Air Transat's spare engine was not available; consequently, a Rolls-Royce loaned engine, previously positioned at the Air Transat facilities, was used.
The engine change, which commenced at midnight on 17 August 2001, proceeded normally up to the point when it was discovered that the rear hydraulic pump (P/N: 974800), taken from the removed engine, could not be fitted onto the replacement engine due to an interference with the high pressure fuel pump inlet tube (P/N: FK12446) already on the engine. A search through the Airbus Illustrated Parts Catalogue (IPC) revealed the existence of a Service Bulletin (SB) RB.211-29-C625. It was then realized that the loaned engine, last certified by Hong Kong Aero Engine Services Limited, was in a pre-SB configuration, and the engine being replaced was in a post-SB configuration. The technician leading the engine change could not access the SB’s from the available computer terminals, and accepted advice from the maintenance engineering department that only the rear, fuel tube from the engine being replaced needed to be used. According to the technicians, a clearance between the fuel and the adjacent hydraulic tube was obtained.

Upon completion of the engine replacement, inspections were conducted by both the lead technician and another technician and no discrepancies were noted. The engine was successfully ground run and the aircraft was released for flight with a post-SB RB.211-29-C664, hydraulic pump (P/N: 974800), a post-SB C625 fuel tube (P/N: FK30383), and a pre-SB C625 hydraulic line (P/N: LJ51006). An examination of the aircraft following the occurrence determined that both engines stopped due to fuel exhaustion, which was precipitated by a rupture of the high-pressure fuel pump inlet fuel tube on the right engine, which failed as a result of hard contact with the hydraulic line. The engine had accumulated 67.5 flight hours since the engine installation.
1.2 Damage to Aircraft
The aircraft first contacted the runway at 1 050 feet from threshold and then bounced for 1 650 feet prior to the second and last touchdown. The touchdowns were sufficiently hard to cause some skin wrinkles on each side of the fuselage just above the main wings trailing edges. Due to the engines-out condition, the landing was conducted without the brake antiskid and normal braking systems. Because the emergency brake accumulator only provides for a limited amount of brake applications, full braking was applied and retained at the second touchdown, resulting in the main wheels locking up. The tires quickly abraded and deflated at a point between about 300 and 450 feet beyond the second and final touch down. The segments of the main wheels contacting the pavement were worn down to the bearing journals, the left, rear, inboard wheel detached from the axle. Both left and right brake anti-torque links attachment horns on the bottom segments of the main oleos also contacted the pavement; the horns were abraded to the point that some of the links separated from the oleo resulting in the rotation of at least one brake carrier.
Shedding of brake and wheel components during the landing run also resulted in a combination of punctures and impact damage to the airframe and left engine nacelle.
正常landing A330 landing speed 係大概~130kt. if flapsless landing might go up to ~170kt. Consider they approaching with200kt, of course the aircraft doesn't want to land. To force the aircraft down his really can't flare or it will take up too much runway. But consider the situation, putting the aircraft down on the runway safely with no casualties is very amazing.(will explain why)
1.6.3 Engine Fuel Tube Rupture
The initial inspection of the right engine following the occurrence uncovered the presence of an L-shaped crack on the inlet fuel tube wall (Part No FK30383). The crack was approximately 3.0 inches (80mm) long and was spread to a width of about 1/8 inches (2.5mm). In addition, the hydraulic outlet tube (pressure) for the rear hydraulic pump was found to be in hard contact with the fuel tube.The cracking on the fuel tube extended to both sides of a mechanically worn (chafed) area where the tubes came into contact. It was evident that the interference and chafing occurred due to the mismatched installation of the post-mod fuel tube (P/N: FK30383) and pre-mod hydraulic tube (P/N: LJ51006). Based on the DFDR data, it was determined that the fuel leak rate through this cracked reached a maximum of about 13.0 metric tons per hour.
有時d parts 裝左上去,仲要check 佢同其他pipe ge clearance. 因為如果有contact point, 當隻機飛ge時候,產生vibration 令喉管摩擦,而摩損~ 呢d損壞唔會即時發生; 好似呢隻A330 換完engine 67.5hr 先開始漏~
8月17日換engine;24日出事~
1.6.6.2 ECAM Indications during the Occurrence Flight
According to the crew, all aircraft systems functioned normally, up to when the aircraft passed 040W at 04:08. No anomalies were noted on the DFDR for this portion of the flight. Of particular note is that at this point in the flight, the right engine oil quantity was stable at approximately 16.0 quarts (18.2 litres11). Oil pressure and temperature are not recorded on the DFDR. At 04:38, the DFDR recorded an increased rate of reduction in the fuel quantity. Analysis of this DFDR data determined that this anomaly was the start of the fuel leak in the right (#2) engine, low-pressure fuel line. The increased rate of reduction in fuel quantity would have been indicated in lower-than-anticipated FOB quantity figure on the E/WD.
At 04:44, the DFDR recorded a decrease in oil quantity on the right engine; however, because the oil parameters were within operating limits an ECAM message was not generated. At 04:56, the DFDR recorded the commencement of a two-minute forward transfer of fuel from the trim tank to the main wing tanks. Total transfer was about 0.3 tons. During this transfer, a green TRIM TANK XFR ECAM message would have been displayed in the memo section of the E/WD. The occurrence crew did not recall seeing this message. According to the crew, at 04:58, shortly after the aircraft crossed 030W, a routine check of the aircraft instrument indications was commenced. It was at this time that the crew noticed that the oil quantity on the right engine was markedly lower than the quantity on the left engine. At 05:04, the crew selected the ENGINE status page on the SD to verify other engine readings.
At 05:11, the DFDR recorded the commencement of a 19-minute forward transfer of the remaining 3.2 tons of fuel in the trim tank commenced. During this transfer, a green ECAM message TRIM TANK XFR would have been displayed. AT 05:21, the crew notified the company operations centre that, although at the beginning of the flight the right engine had 18.5 litres of oil, the oil quantity was now only 14.5 litres, the oil temperature was 65 degrees Celsius, and the oil pressure was 150 pounds per square inch (psi); these readings were significantly different from the readings on the left engine, which were 18.2 litres, 110 degrees Celsius, and 80 psi. MCC advised the crew that the problem would be analysed and that the flight would be contacted with the results. The readings were within the parameters specified in the Engine Oil Consumption Airbus A330 chart. At 05:30, the trim tank forward fuel transfer was completed and a TRIM TANK XFRD message would have appeared in the memo section of the E/WD; this message would remain displayed for the duration of the flight. The complete forward transfer of the trim tank fuel is not scheduled to occur until 35 minutes from the destination airport, until the wing tanks are below 4.0 tons, or until the aircraft descends below FL 245. At 05:33, a pulsing, white ECAM advisory ADV message was generated and displayed in the memo area of the E/WD, indicating a 3 000 kg fuel imbalance between the right and left wing tanks. Under normal conditions, this ECAM advisory brings up the FUEL system page on the SD. However, the manual selection of ENGINE systems page by the crew inhibited the display of the fuel page. A 3 000 kg fuel imbalance is an abnormal condition that does not result in a display of the corrective action required to correct the imbalance. To ascertain the required corrective action, the crew must view the fuel page, diagnose the pulsing fuel quantity indications, and then refer to the appropriate page in the Quick Reference Handbook (QRH). At 05:34, the crew deselected the ENGINE page, and the FUEL page was displayed in the SD. At 05:36, having noted the fuel imbalance, the crew opened the crossfeed valve and turned off the right-wing fuel pumps, establishing a crossfeed from the left wing tank to the right engine. An amber FUEL R WING PUMPS LO PR message would have appeared on the left side of the message area of the E/WD and a green WING X FEED memo would have appeared on the right side. Shortly afterward, the crew also noted that the remaining fuel on board was significantly below the planned quantity. Fuel losses or leaks themselves cannot be identified as such by the ECAM system; consequently, a specific ECAM warning is not generated for these conditions, although related system messages would be generated as normal parameters were approached or exceeded. At 05:52, the caution message ENG 2 FUEL FILTER CLOG appeared on the E/WD. This message indicated an abnormal (and sometimes temporary) pressure loss across the fuel filter of the right engine. This type of message does not require action by the crew; it is only generated for crew awareness and monitoring, if necessary.
The crew first notice the problem with Low Engine Oil Quantity, Low Oil Temp and High Oil Pressure.
That's a natural instinct for all pilot to aware of the engine parameters, especially the Engine oil; because that would be an early indication of engine failure. However, normally during oil leak, the indication would be High oil temp, low oil pressure; which is opposite to the case, and the pilots are confused. And suspecting computer/sensor error. They were so focus on figuring out the abnormal oil parameters, as abnormal oil parameter might lead to engine shutdown; they did not put to much attention to fuel imbalance. Opened the crossfeed and transfer fuel to leaking tank and eventually lead to fuel starvation.
At 05:54, the crew established crossfeed from the right-wing tank to the left engine by selecting the right-wing pumps ON and the left-wing fuel pumps OFF. A FUEL L WING PUMPS LO PR message appeared on the left portion of the E/WD message screen and the WING X FEED memo would have continued to appear on the right portion. At 05:58, the FUEL R WING TK LO LVL message appeared, indicating less than 1 640 kg of fuel remaining in the right inner tank for more than 60 seconds. At 06:08, the FUEL L+R WING TK LO LVL message appeared, indicating that inner tanks on both wings were now below 1 640 kg for more than 60 seconds. At 06:13, the ENG 2 STALL and ENG 2 FAIL messages were displayed indicating that the right engine had flamed-out. The RPM decay resulted in the ENG 2 STALL message; the ENG 2 FAIL message indicated that core speed had decelerated to below idle with the master switch ‘on’ and the fire pushbutton ‘in’ (not pushed). At 06:21, the FUEL TRIM TK PUMP LO PR message was displayed indicating that the trim tank transfer pump switch had been selected to FWD and no fuel remained in the trim tank. At 06:26, the ENG 1 STALL and ENG 1 FAIL messages were generated as the left engine flamed-out. As the associated generator decelerated, the aircraft would have automatically reverted to the emergency electrical configuration, with power supplied by the automatic extension of the ram air turbine. The EMER ELEC CONFIG warning may have been inhibited by the ENG ALL ENG FLAMEOUT warning; neither warning was recorded on the Post Flight Report. 1.6.7 Flight Management Guidance Computer The A330 aircraft is equipped with a Flight Management Guidance Computer (FMGC). The flight management part of the computer performs four main functions: navigation, flight planning, prediction and optimization of performance, and management of displays. Predictions are displayed on the Multi-purpose Control Display Unit (MCDU). When making fuel remaining predictions for an aircraft in flight, the FMGC, in part, takes into account the fuel currently on board, flight plan, planned vertical profiles, predicted times, and fuel flow to operating engines. The estimated fuel on-board at destination (EFOB) prediction would not take into account fuel being lost as the result of a fuel leak. On the occurrence flight following the annunciation of the fuel imbalance advisory, the crew, on a number of occasions, referred to the predicted fuel remaining on board at destination figures presented on the MCDU to make decisions. By not taking into account the fuel leak rate, the FMGC would have predicted fuel reserve quantities significantly above what would actually occur, and the EFOB at destination would have been constantly decreasing. The FMGC would have displayed minus quantity when a diversion was a priority.
1.6.8 Electrical Systems
The A330 aircraft electrical system is normally powered by two engine driven generators. The aircraft also has three 24-volt batteries. The aircraft’s electrical network can also be supplied by the APU generator. These three generators are all identical and any one of them can supply the entire aircraft electrical needs. As a backup, there is a hydraulically driven emergency electrical generator, which is powered by the green hydraulic system. In the event of a severe electrical failure and a lack of hydraulic power to actuate the emergency generator, a Ram Air Turbine (RAT) can be automatically or manually deployed to provide the hydraulic pressure to power the emergency generator. During the RAT extension, the electrical system is powered from the batteries. On the occurrence flight, as a consequence of the double-engine failure, the aircraft lost both engine-driven generators and hydraulic pressure, and the RAT was deployed. This deployment resulted in the aircraft electrical system being supplied by the emergency generator. This configuration resulted in the loss, in part, of the following electrical services: Flight Guidance Management Computer, Multipurpose Control and Display Unit, HF 1 radio, Cockpit Voice Recorder, Flight Data Recorder, Auto-pilot 2, Flight Control Data Concentrator 1, flaps, pitch trim, rudder trim, Navigation Display 1, Auto Break/Anti Skid, Distance Measuring Equipment, and standby altimeter lighting. In preparation for landing, in accordance with the ENG ALL ENGINE FLAME OUT, the crew selected the LAND RECOVERY push button and selected FLAP 1, which extended the slats. At slats extension, the emergency generator was inhibited and the electrical supply automatically transferred to the batteries. The approximate flight time on batteries is 30 minutes.
Airbus 有2個complex failure, Electrical Emergency Configuration 就係其中之一.
1.6.9 Flight Controls
The Airbus A330 is a new generation aircraft that utilizes fly-by-wire technology, in that the flight control surfaces are electrically controlled and hydraulically activated. Some surfaces, like the stabilizer and the rudder, can be mechanically controlled. Three independent hydraulic systems are used to power all the flight control surfaces. Five flight control computers process pilot and autopilot inputs according to normal, alternate or direct flight control laws: three Flight Control Primary Computers (FCPC) and two Flight Control Secondary Computers (FCSC). Two Flight Control Data Concentrators acquire the data from the FCPCs and FCSCs and send the data to the Electronic Instrument System (EIS) and Central Maintenance Computer (CMC). On the occurrence flight, the flameout of both engines resulted in the loss of the BLUE and YELLOW hydraulic systems. The GREEN hydraulic system continued to be powered by the RAT. Loss of the BLUE and YELLOW systems results in the following inoperative systems: Flight control protection (degradation), stabilizer, auto-pilot 1 and 2, most spoilers, alternate brakes, yaw damper 2, nose wheel steering, and reversers. The HYD B + Y SYS LO PR procedure states that pitch authority will be reduced, and suggests that the flare for landing must be started earlier and that more stick deflection might be needed to achieve the flare. The reversion to emergency electrical power also resulted in the loss of pitch and rudder electric trim.
而另一個complex failure 就係Dual Hydraulic Failure. 同時要handle Both Engine shutdown + Elec Emer Conf + Dual Hydraulic. 可想而知個workload 有幾大~
1.19 Aircraft Operational and Operational Factors
1.19.1 Cockpit Management
The captain of an aircraft has overall responsibility for the safe operation of the flight. In a two-man cockpit, one pilot is designated as Pilot Flying (PF) with the other pilot being Pilot Non Flying (PNF). Regardless of the allocated duties, the crew must work as a team, and this requirement is a basic part of Crew Resource Management (CRM) training. A basic element of CRM is that, whenever possible, the situation must be fully understood and agreed to by the crew before any corrective action is taken. In accordance with the instructions detailed in Air Transat A330 Flight Crew Operating Manual (FCOM) 3, the Abnormal and Emergency procedures represent the actions applicable after a failure, to ensure adequate safety and to ease the further conduct of the flight. They are applied following the “READ and DO” principle.
1.19.2 Fuel System Abnormal Procedures
The integrity of any abnormal procedure relies on the premise that only the correct procedure should be used for a given situation, and that the procedure should be completed in its entirety. On the A330, most procedures are displayed on the ECAM, and as each procedure item is properly completed, the item is removed from the display screen. Crews are taught to trust that the ECAM system will alert them of significant events that could have an effect on safety, and that completing the prescribed procedure will best ensure safety of flight. Neither the FUEL IMBALANCE procedure, nor the FUEL LEAK procedure, is displayed on the ECAM.
A330 ECAM can only detect fuel imbalance;but not able to detect fuel leak. (An improvement on A350 has been made.)
1.19.2.2 Fuel Leak
A FUEL LEAK is an abnormal condition that is not monitored by the ECAM system; consequently, an ECAM warning is not generated for these conditions. Instead it is expected that the crew’s normal monitoring of the fuel system parameters will result in timely recognition that a fuel leak exists or a loss is taking place, and the conclusion that actioning of the FUEL LEAK procedure is required. The only other catalyst that would result in the crew referencing this procedure is the CAUTION note in the FUEL IMBALANCE procedure.

When the conditions of a fuel leak have been ascertained, the crew is required to refer to the appropriate page in the Quick Reference Handbook (QRH), and required to complete the procedure items. The FUEL LEAK procedure is specifically designed to specify the actions required to mitigate the consequences of a fuel leak affecting either side of the fuel system. The conditions that would suggest the presence of a fuel leak are contained as notes at the top of the procedure items. Other than in the FUEL LEAK procedure, the only other reference to fuel-leak symptoms and the fuel leak procedure in a manufacturer or company documentation is in the Air Transat FCOM Volume 3, Standard Operating Procedures (SOPs), relating to flight progress monitoring. Section 03.03.15, in part, requires that, when overflying a waypoint, crews check that the sum of the fuel on board and the fuel used is consistent with the fuel on board at departure. Crews are directed to suspect a fuel leak if the sum is unusually smaller than the fuel on board. A fuel leak is considered to be an abnormal condition that would rarely, if ever, occur. Other than the procedure itself and the reference in the SOPs, no manufacturer or company documentation exists on the use of this procedure, and no training is provided for this abnormal situation.
The crew stated that, although indications of a lower-than-expected fuel quantity were recognised shortly after receiving the fuel imbalance ADV, they did not consider the FUEL LEAK procedure, until later in the flight.
1.19.2.3 Fuel Tank Low Quantity
A fuel tank low level ECAM Caution is generated by the ECAM system when the fuel quantity in the right or left wing tank is less than 1 640 kg for 60 seconds. This condition results in a MASTER CAUTION light and a crew action item procedure and the relevant system synoptic page to be displayed on the SD. The graphic depicts the wing tank low-level procedures taken from the QRH. Although the FUEL L(R) WING TK LO LVL procedure contains a caution directing that this procedure is not to be applied if a fuel leak is suspected, the Caution does not appear on the procedure generated on the E/WD. Both the FUEL L(R) WING TK LO LVL and the FUEL L + R WING TK LO LVL procedures ultimately call for the WING X FEED to be turned ON. On the occurrence flight, the caution and associated ECAM messages and procedure were generated at 0558 for the FUEL R WING TK LO LVL condition and at 0608 for the FUEL L + R WING TK LO LVL condition. The crew did not take any action in direct response to either of these messages.
1.19.3.5 Crew’s Awareness of the Fuel Leak
According to the crew, the following factors were taken into account to ascertain the problem of the unexplained low fuel quantity: • Engine indications were reviewed to determine a source of the problem. No abnormal indication was found. Fuel-flow parameters and other engine indications were normal. • There had been no other in-flight events or conditions that could have led to the fuel loss. • The cabin crew were asked to visually check outside the aircraft in the vicinity of the wings and engine for signs of a fuel leak, and none were observed due to darkness that prevailed during this time. • From the time when the fuel imbalance ADV first appeared, the fuel quantity indications and fuel predictions for destination consistently showed an unbelievable fuel loss rate.
The crew stated that because there were no other signs of a fuel loss, other than the lower than expected quantity of fuel on board, and because there had been no other ECAM warnings or cautions both pilots believed that the problem was a computer fault. They also stated that although they had used the term “fuel leak” on many occasions during the occurrence, a logical link to considering the FUEL LEAK check and the possibility that the fuel leak existed did not occur until the aircraft indicated fuel quantity was about 7 tons. When considering the FUEL LEAK procedure, the crew was of the opinion that the leak was probably on the right side, and that the leak was probably from the tank because the right engine was running normally and all engine indications were within limits. The Captain stated that he had decided not to do the FUEL LEAK – LEAK NOT FROM ENGINE procedure because in his mind doing so would require him to descend the aircraft to 20 000 feet, and if the leak was real, he would be losing fuel anyway, and at 20 000 feet he would give up altitude and performance margin in a situation where fuel remaining was critical. Also, if the leak was from the right tank, he could conserve that fuel by crossfeeding it to the left engine. Consequently, he opted to remain at FL 390 and crossfeed from the right tank. The crew stated that they continued to believe that the low quantity indications were caused by some type of computer error, and continued with this belief up to and beyond the flameout of the right engine.
1.19.8 Engines-out Approach and Landing
From the time that the diversion to Lajes was initiated up to the time that the second (left) engine flamed out, the crew was using the FMS system for navigation guidance. Also, based on the CVR, the crew had visual contact with ground-based lights in the direction of Terceira Island when the aircraft was descending through flight level 370 and at 120 nautical miles northeast of Lajes. Once normal electrical power was lost, the crew no longer had the FMS and had to rely on directional guidance based on the LM VOR and distance information provided by Lajes Approach Control. The crew acquired visual contact with the runway with the assistance of the flashing of the runway lights. The Captain reported that he had the flashing runway lights visually from a long way out and that he was confident that he had more than enough altitude to glide to the airport. Consequently, during the initial glide, he was attempting to fly the aircraft at a speed, between the recommended glide speed and the stall-warning speed, in order to keep the aircraft airborne for the longest time. Other considerations taken into account during the glide were that the aircraft speed could not be higher than 200 knots for gear lowering, the recommended approach speed was 170 knots, the minimum speed to ensure RAT operations was 140 knots, and that he had to adjust the aircraft pitch angle to achieve a glide descent angle to reach the runway. Although he had never received formal training on gliding approaches, he had experienced doing power-off approaches to landing in a number of aircraft types that he had flown. The Captain reported that during the glide that he did not use manual trim, because he was very busy concentrating on maintaining the correct vertical profile to the runway. In addition, although he knew that the aircraft response to stick inputs would be sluggish, during the flare he did not want to be too aggressive. Following the initial bounce, the nose of the aircraft rose significantly. Because he did not want to become airborne a second time, on the second touchdown, he did not flare and he applied and held maximum braking.
Lesson learn: Don't take fuel imbalance easily. CHECK if there is fuel leak before open the crossfeed. The imbalance would affect the handling a bit; but at least both engines running, so there is no need to rush. In fact, as I learn from my favorite Captain, he taught me not to rush (except uncontrollable FIRE, SMOKE and BOMB onboard.) Besides these, No need to rush. Confirm the failure before acting on it.
At last, I made a little flow chart to fuel leak procedure. Enjoy and Fly safe~
